Structures
Numerical and multi-scale modelling
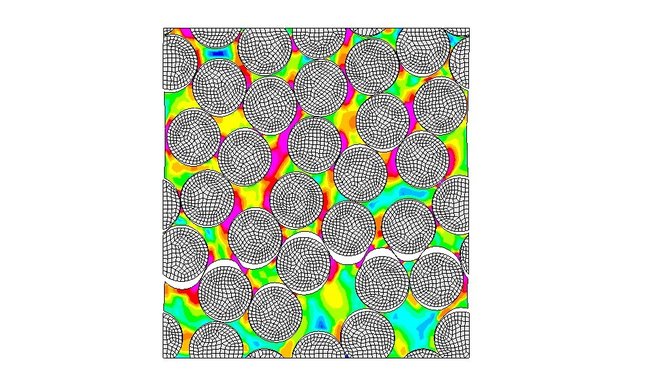
Bristol Composites Institute has a long tradition of development and application of high quality numerical models. Novel technology developed includes cohesive interface elements (especially with additional functionality such as fatigue, through-thickness reinforcement), new element formulations e.g. for mesh independent crack prediction and fast, accurate prediction of complex stress fields. The application of our models is wide ranging, including high fidelity simulations of composites failure, micro-mechanics simulations of reinforcement, impact, fatigue, and hygro-thermal effects. Since composite failure is often driven by small scale features, the prediction of failure at structural scale is challenging. For this we have developed multi-scale modelling techniques that allow the fine scale features at ply level to be captured, which would otherwise not have an effect in homogenised models.
Contact: Professor Stephen Hallett
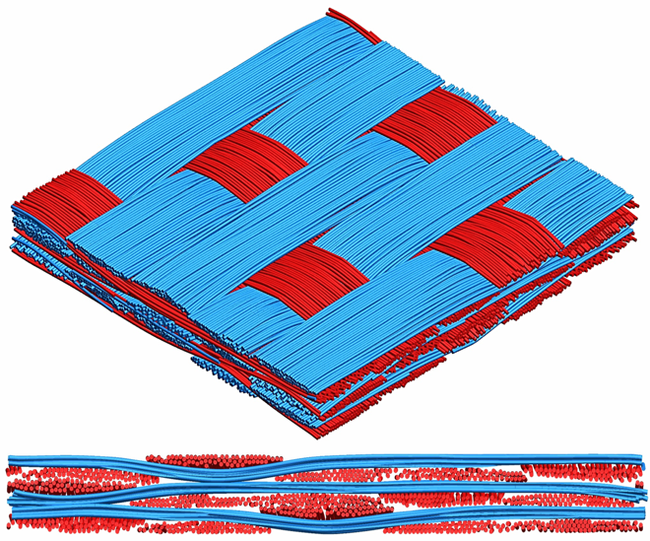
Our work on textile reinforced composites covers novel numerical methods for prediction of stiffness, strength and internal geometry. For accurate strength predictions it is important to have a realistic representation of the as-woven and final infused composite preform geometry, as this strongly influences the results. We have developed numerical techniques for prediction of preform geometry for a wide range of fabric reinforcements, including 2D woven, 3D woven, NCF and braids. A particular focus of our models for strength prediction is for complex internal geometry such as encountered in 3D woven materials and scale up of methods, beyond unit cells, to structural and component scale.
Contact: Professor Stephen Hallett
Optimization of composite structures
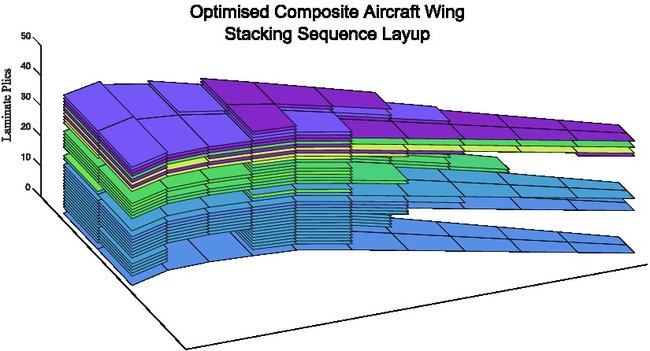
Structural optimisation draws on a powerful set of tools and methods enabling us to effectively exploit the directional strength and stiffness of fibres resulting in high performance composite structures. Determining optimal topologies, stiffness, strength, and mass distributions of composite structures are common goals of the optimisation process, which often have to be balanced against performance and cost requirements of the system. Numerically, major challenges remain to be solved and currently no computationally efficient algorithms able to design optimal manufacturable composite structures exist. That is, in part, due to the extremely large, discrete, and non-linearly constrained design space associated with the optimisation of complex systems. However, it is clear that composite materials have a role to play in the structural design of components for aerospace, automotive, civil, and energy industries. As such, our research focuses on the use and development of innovative design and optimisation methods aiming to demonstrate the potential of composites and facilitate its use in industrial applications.
Contact: Dr Terence Macquart
Elastic tailoring of composite structures
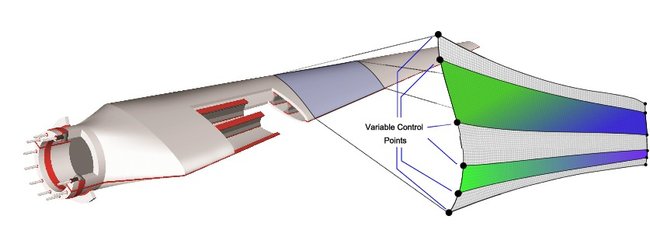
Designing high performance yet cost-effective structures is of paramount importance in competitive markets such as aerospace and wind energy. Elastic tailoring is about exploiting the anisotropy of composite materials to achieve structurally efficient designs, in the simplest case resulting in the alignment of fibres with critical load paths, or deformation modes. By taking advantages of the significant tailorability of composite materials, we can design structures that behave, globally and locally, according to our requirements. Ongoing work involves analytical, finite element and experimental investigation of buckling and post buckling, morphing and deployable structures, aeroelastic tailoring of aircraft wings and wind turbine blades.
Contact: Dr Terence Macquart
Effects of defects and features
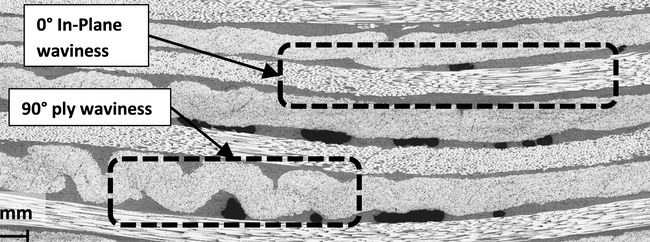
Composites manufacturing processes can lead to a wide range of possible defects in a final structure, e.g. wrinkles, voids, resin rich regions, distortions. Also, certain geometric features are a necessary part of component design, such as ply terminations to reduce part thickness. Both defects and features can have an effect on the strength and performance of a composite component and so it is important to understand and be able to predict their role the initiation of failure. Our experimental work has created a range of controlled levels of defects, that allows their characterisation. An important part of the characterisation of defects is their non-destructive evaluation, through techniques such as X-ray micro computed tomography (CT) scanning and ultrasonic inspection. We have developed high fidelity finite element models that can accurately predict strength knockdowns from known defect severities.
Contact: Professor Stephen Hallett
Through-thickness reinforcement
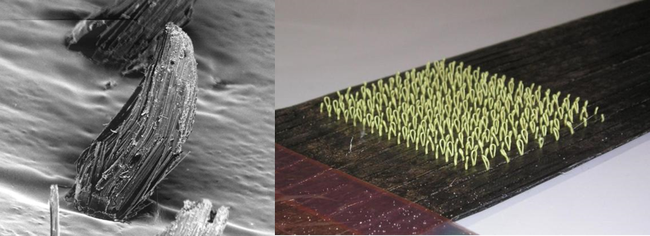
Through-the-thickness reinforcement of polymer matrix composites utilises solid rod-like microfasteners to create effective barriers to interlaminar crack propagation. Both carbon fibre Z-pins (on the left) and thread-like tufts (on the right) have submillimetre diameters. The former is best suited to reinforcing composites made from prepregs while tufting is a one sided stitching technique compatible with manufacture of dry fibre preforms.
Contact: Professor Ivana Partridge
Fatigue
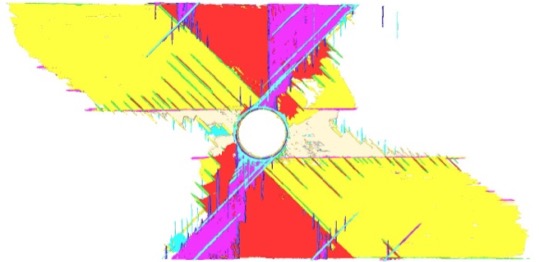
Whilst composites are considered better than their metallic counterparts at resisting the effects of cycling loading, under very high numbers of cycles or high loading severities, they can still be prone to fatigue damage. This is particularly so for the case of delamination, where there are no reinforcing fibres in the through thickness direction. Damage can initiate at load levels well below ultimate static strength and propagate, leading to catastrophic failure. Our work on fatigue has characterised fatigue damage growth in a number of scenarios, e.g. from open hole stress concentrations, wrinkle defects, cyclic loading of z-pin through-thickness reinforcements and fully reversed (R=-1) loading. We aim to understand the fundamental phenomena driving the development of fatigue damage and also develop novel numerical models that allow us to predict performance under cyclic loading.
Contact: Dr Luiz Kawashita
Ductility in composites
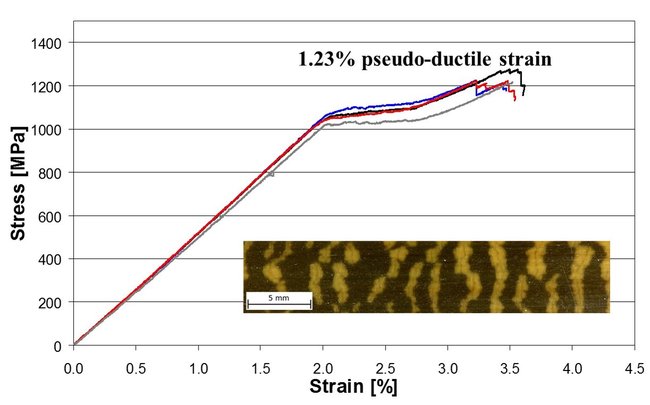
A number of novel approaches are being explored to create composites that fail more gradually, with a ductile or pseudo-ductile response. Hybridisation, fibre reorientation and discontinuous architectures are able to produce stress-strain responses with a plateau rather than catastrophic failure, and less sensitivity to stress concentrations. Damage can be observed visually whilst load is still carried safely. We are developing new concepts, exploring the properties of these materials and working on applications where greater tolerance of damage and easier detection will open up new opportunities for composites.
Contact: Professor Michael Wisnom
Morphing and non-linear structures
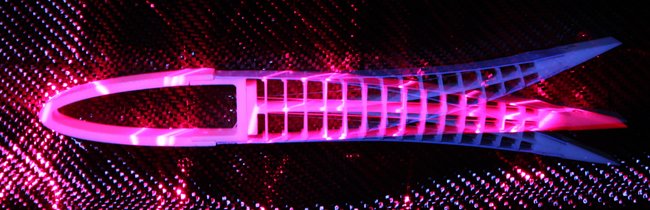
We develop advanced structures that rely on large deflections and nonlinear mechanics to achieve higher structural efficiency and introduce new functionality. For example, morphing structures can change their shape to operate efficiently in multiple operational regimes and thereby increase performance. Our work focuses on gaining physical insight into the non-linear behaviour of these systems and how best to exploit their properties. We address the many new challenges across the range of analytical and numerical modelling techniques, and subsequent experimental validation. By carefully controlling the nature of the non-linear behaviour, it is possible to produce well-behaved non-linear structures with repeatable elastic responses that are well-understood and can be matched successfully with experimental demonstrators. Applications can be found in a range of areas, such as morphing aircraft, wind turbine blades, adaptive air intakes and medical devices.
Contact: Dr Mark Schenk