HiPerDiF (high performance discontinuous fibre) technology, invented at the University of Bristol, produces highly aligned discontinuous fibre composites with the goal of addressing the issues of the composite industry - manufacturing and recycling.
HiPerDiF capabilities
Fibre alignment
HiPerDiF technology employs a series of fibre-water jets aimed perpendicular at an array of slotted plates.
Each fibre-water jet has a corresponding plate. The momentum change of the fibre-water jet on the plates aligns the fibres, parrallel to the plates.
The fibres are deposit on the mesh conveyor belt and water is removed via a vacuum pump.
Drying stage
The use of water as a dispersing agent leads to easy removal of water from both synthetic fibres and natural fibres using a combination of vacuum and IR heating.
Preform fabrication
A combination of preforms can be fabricated using a diverse range of fibres; natural, synthetic (virgin and reclaimed), along with thermosetting and thermoplastic matrices
Comparison to long fibres: Aligned discontinuous fibre composites with 85% of the fibres aligned within ±5⁰ from perfect alignment led to comparable properties to continuous fibre composites, using HiPerDiF [1].
Figure 1. Mechanical properties of ADFRC from HiPerDiF [1]
Pseudo-ductility: Hybrid composites (intermingled [2], intraply [3] and interlaminated [4][5]) achieved pseudo-ductility through fragmentation and diffuse debonding/delamination.
Fig. 3. Intraply hybrids [3]
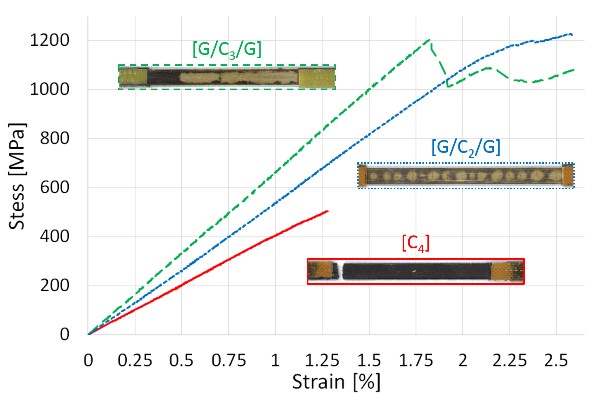
Recycling & Sustainability: Composite recycling is a two-step process: the degradation of the matrix to reclaim the fibres and their remanufacturing in a new recycled material. Independently from the matrix degradation processes the reclaimed fibres are in a filamentised, random, low-density-packing form. The HiPerDiF technology allows to remanufacture them into high fibre volume fraction recycled composites with outstanding mechanical performance [8],[9],[10],[11] & [12].
Fig. 5. Life-cycle of fibre composites with HiPerDiF
Moreover the technology allow the processing of natural fibres to obtain sustainable composites [13].
HiPerDiF can process natural fibres. Intermingled flax and re-claimed fibre (rCF) composites demonstrated damping and a cost reduction compared to a pure carbon fibre composite.
It is possible with HiPerDiF to vary the quantities of each fibre type and the type of hybrisation (i.e. intermingled, interlaminated etc.), allowing the design engineers to tailor the mechanical, functional properties and the cost.
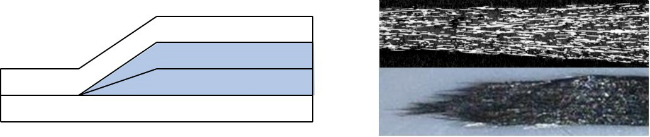
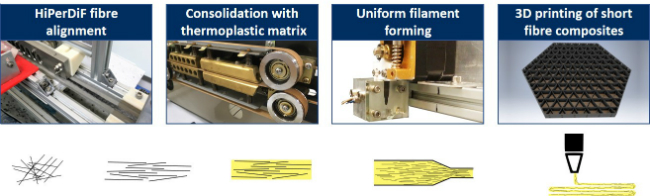
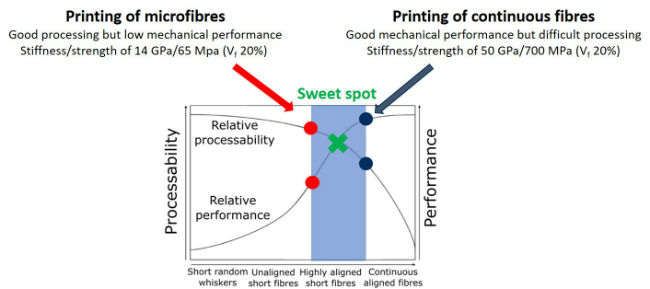
The HiPerDiF technology was invented during the EPSRC funded HiPerDuCT programme.
This research was funded by the UK Engineering and Physical Sciences Research Council (EPSRC) the EPSRC “High Performance Discontinuous Fibre Composites—A sustainable route to the next generation of composites” grant number [EP/P027393/].
All HiPerDiF related publications can be found at: https://www.researchgate.net/project/HiPerDiF-High-Performance-Discontinuous-Fibre